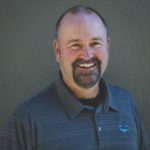
“It’s surprisingly easy to make your own custom pattern—especially with Dave breaking it down step by step in this demonstration.”
Trade education and workforce development are two initiatives we value highly here at Dunn Lumber, so it should come as no surprise that we have close ties with Seattle Central College's Wood Technology Center (WTC). With roots dating back to the early 1900s, WTC's history intersects with ours at Dunn Lumber at various points (our very own Ed Dunn Jr. took some classes at Edison), and we're proud to be connected with such an exemplary educational institution.
Throughout the episodes in this series, we'll be speaking with Dave Borgatti, a long-time faculty member at the WTC, about the center's history, program offering, and various topics in woodworking education. Dave got his start in woodworking as a boat builder in Portland, Oregon, for Schooner Creek Boat Works, and ended up at WTC as an instructor in 1992. Since then, Dave has helped countless students—from boat builders to carpenters and cabinetmakers—learn the woodworking craft.
You’ve probably heard about using templates or patterns in woodworking to help create a unique shape or replicate cuts. Today, Dave shows us how simple it can be to create your own pattern through a quick but highly informative demonstration.
When do you need a woodworking pattern?
Woodworking patterns or templates are often used for projects that require multiples of the same piece, or projects that may be built again in the future. They’re also often used when building or fitting countertops and cabinets.
Materials needed to make a woodworking pattern
Patterns can be made out of different materials depending on the project or use. Here, Dave shows us how to quickly create patterns using a few common materials:
- ⅛” lauan plywood, sometimes called "doorskin" (a thin, brittle wood that can easily be scored with a blade and snapped in two)
- Hot glue
- Utility knife
- Fender washer (if following a curved edge)
- Jigsaw (if cutting a curved edge)
- Block plane (if creating a curved edge)
- Sharp pencil
How to make a woodworking pattern
As Dave demonstrates in the video, you can make a pattern quickly and cheaply with simple tools and materials. He’s creating a pattern that has four corners, two straight sides, one angle side, and one curved side to show how to handle different shapes.
Key points to keep in mind:
- You want your template pieces to fit closely in the corners, but they don’t need to be exact—you’ll naturally create the correct corners when you use the temple to cut a piece.
- The template pieces need to overlap sufficiently so that you can glue them together.
- Fender washers are larger than normal washers. By placing the pencil inside, it will follow any irregular surface.
- To create a curved edge, position the lauan plywood as close to the correct place as possible, then use a washer and a pencil to mark the curve. Dave shows how to do this starting at 05:50 in the video. When you have the curve marked, you can then use a bandsaw or jigsaw to cut close to your curved line. Then, smooth out your cut with a block plane.
- When your pattern is done, make sure to mark which pieces are the top, bottom, right, and left sides on the front-facing side of your pattern.
- You also want to add some simple gussets in the corners, using the lauan plywood, to strengthen the template so it doesn’t snap in transit to your work site.
And there you have it! It really is that simple, and you can always come back to this video as a refresher to see how Dave does it.
If you’re looking for other woodworking demonstrations, check out our other Wood Technology Series conversations with Dave, including going over how to use a biscuit joiner and how to calculate board measure.